Created as a pathway for the University of Auckland’s research to connect directly to real world applications and industries, the Creative Design and Manufacturing Lab (CDAML), opened in 2019, focuses on the development of 3D printing as a mainstream method of production rather than a tool for rapid prototyping.
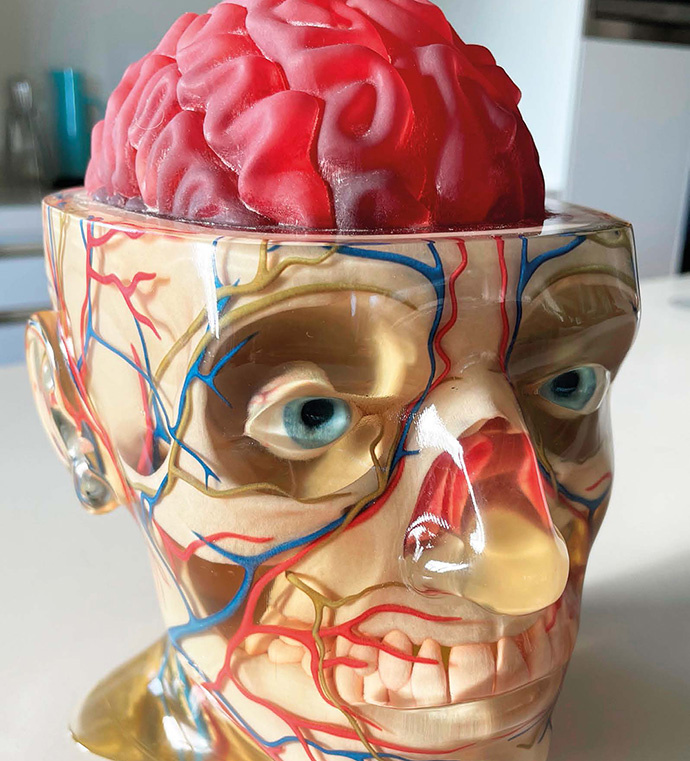
The 3DUJ-553 has opened the CDAML to medical applications such as visual aids for doctor-patient communication
With 4 permanent staff and over 20 PhD, postgraduate, and undergraduate students from different disciplines working in the lab, a wide variety of research projects are undertaken.
Some include high efficiency gyroid based heat exchangers, automated designs for prosthetic sockets, and 3D printed food supplements from meat powder for the elderly.
The CDAML also functions as a 3D printing service provider and educator to external industries, helping businesses expand their production opportunities through additive manufacturing.
The lab started out with several powder-based 3D printers, focusing on projects in engineering, but Professor Olaf Diegel, the Director of the Creative Design and Additive Manufacturing Lab, had wanted to add color from the start “We always wanted color, but we made do without.”
He had worked with a gypsum-based full color 3D printer in the past, but the parts created were so brittle that they couldn’t be utilized in any way “If you looked at the part sideways, they would break.”
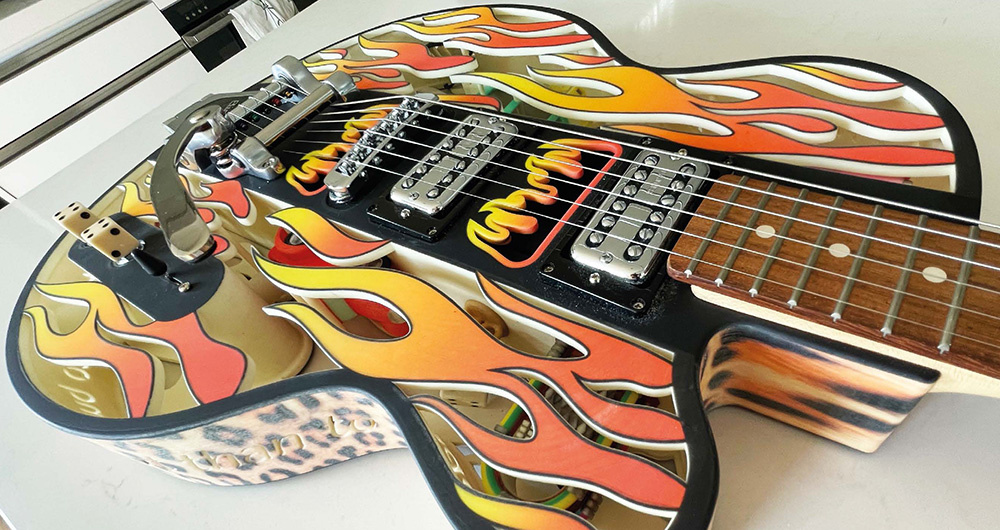
The American Graffiti 2.0 guitar printed in full-color on the 3DUJ-553, eliminating the need for hand painting
At first, the lab used what they had available and hand painted parts that needed color. But the turning point for him came while pursuing a personal project. Professor Diegel has been designing and 3D printing fully functioning guitars for the past ten years to see how he could push the limits of 3D printing. “About 2 years ago I did a Beatles themed base guitar, inside the guitar there is a yellow submarine, an Abbey Road scene, Sergeant Pepper’s drum kit, and my wife, who is an artist, hand painted the inside of it for me. By the end I think she hated me!”
Professor Diegel connected with Mimaki USA to collaborate on another guitar in 2020. With the help of the 3DUJ-553, he was able to print a full-color body for a fully operational electric guitar, the Scarab ST.
After printing his Scarab ST Guitar on the 3DUJ with Mimaki USA, he knew what printer to add to the lab. “It came out looking stunning...so good that it is what caused us to buy the printer.”
He had also printed the guitar with two other full-color 3D printing technologies (an inkjet type and a nylon-based printer), but the colors on the 3DUJ-553 came out the most vibrant.
The biggest deciding factor for the university however was the running cost. ”For universities, it’s not really the price of the machine, but the ongoing costs.” When Professor Diegel was looking at comparable printers, he noticed their material cost was almost double that of the 3DUJ-553.
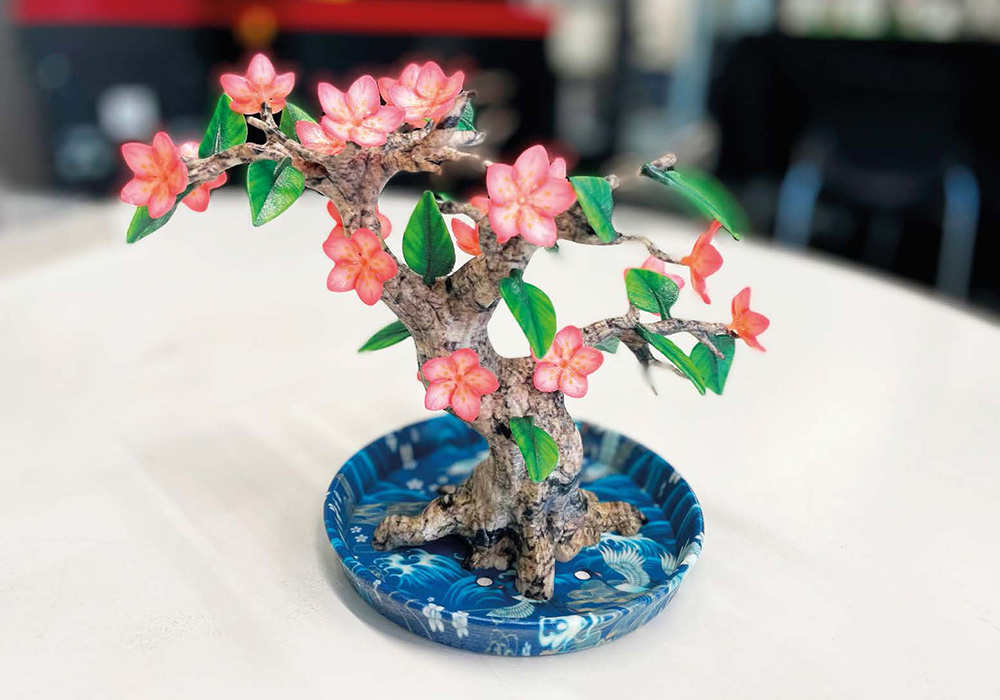
A bonsai tree made during one of CDAML's "Creative Fridays"
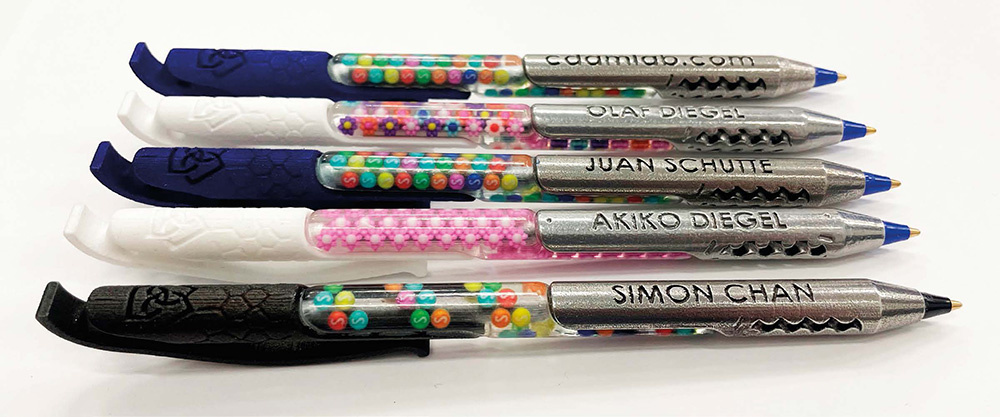
Created by Juan Schutte (PhD), these pens were printed with three different 3D printing technologies including the 3DUJ-553
Professor Diegel says the 3DUJ-553 has undoubtedly brought in new students to the university and created more interest in the lab for current students. “The color prints are what draws people in during the open days”. Although 3D printing is typically used by engineers within the university, the 3DUJ-553 has also opened the lab up to art students as well.
Installing the 3DUJ-553 has also added new applications to the CDAML’s printing services, including 3D scanned human figures, full color prototyping and mockups, as well as medical modeling. Outside the university, doctors are using the lab’s print service to model visual aids for surgeries from patient CT scans.
Professor Diegel explained that doctors use the models to communicate procedures to patients to reduce uncertainty about operations. Because of this, more opportunities have come in from the medical industry, utilizing not only the 3DUJ-553, but the facilities’ other printers as well.
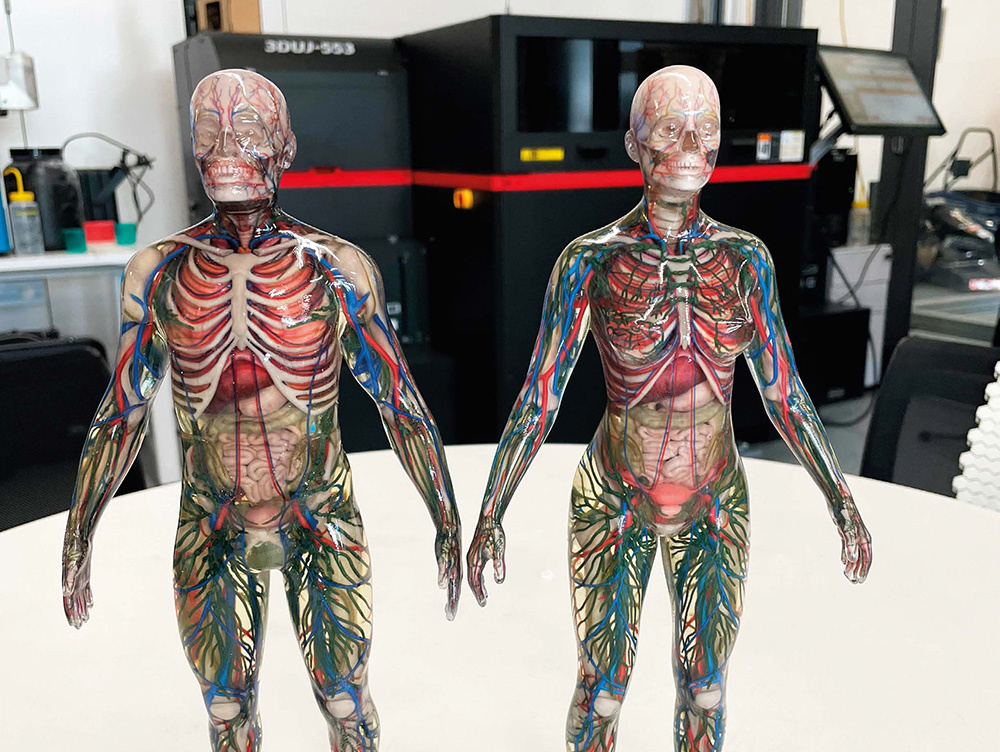
"Life in plastic, it's fantastic: 3D printed anatomical models" won the CDAML an engineering creativity award in 2021
Another project the lab has decided to take on that was impossible before installing the 3DUJ-553 involves replicating Māori artifacts through 3D scanning and printing for cultural preservation. They recently scanned a conch shell trumpet, an heirloom of a Mauri family, and printed it into a playable full color replica.
The CDAML is looking forward to the future of the 3DUJ Series, especially for medical applications, hoping to someday make ultra-realistic models for surgical practice that accurately replicate the original.
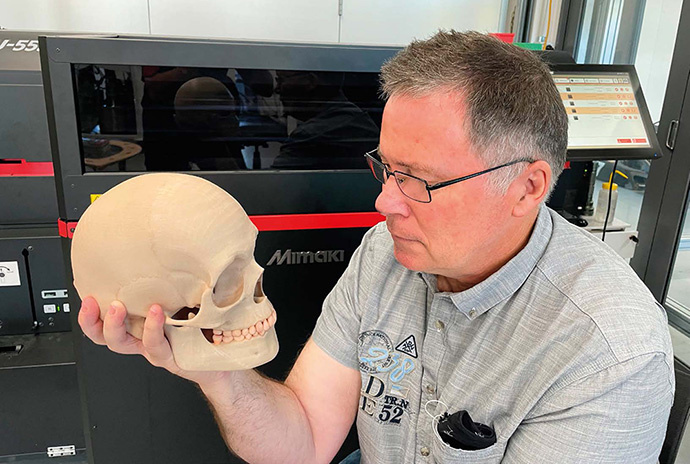
Professor Olaf Diegel contemplating the next full color project
User profile
- NameCreative Design and Additive Manufacturing Lab at the University of Auckland
- AddressBuilding 901-324, University of Auckland Newmarket Campus, 314-390 Khyber Pass Road, Auckland, 1023, New Zealand
- URLhttp://www.cdamlab.com/